Performance Improvement
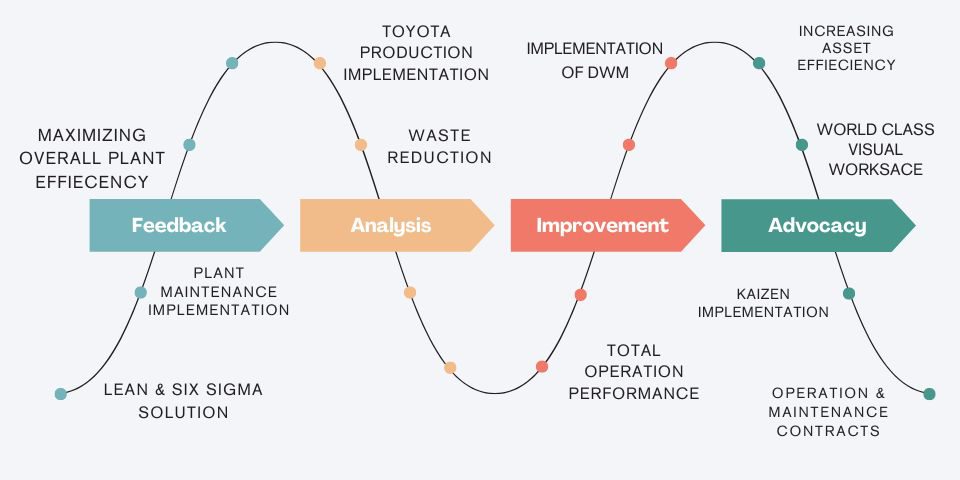
Maximizing Overall Plant Efficiency (OPE/OEE)
Overall equipment effectiveness (OEE) solutions are designed to help manufacturing businesses like yours optimize processes and get the most out of both machinery and personnel to maximize efficiency and productivity.
Toyota Production System Implementation
TPS improves quality in products and processes. Overall, TPS uses several lean methods to help reduce errors and improve quality: Kaizen, 5S, 5 Whys, and Poka-Yoke. These tools help workers spot inefficiencies, errors, or potential defects and empowers them to stop the assembly line so that defects are not included in the final product.
Jishu Hozen & Plant Maintenance Implementation
The primary benefit from implementing Planned Maintenance is the reduction in breakdowns, which leads to reduced cost and improved machine efficiency. The pillar will also contribute to improved quality and safety performance.
Lean & Six Sigma Solutions
Six Sigma is a set of methods and tools for process improvement. Developed in 1986, Six Sigma has become a global phenomenon with companies around the world. Companies and individuals are using six sigma methodologies to improve operational efficiencies.
Total Operational Performance (TOP)
The concept is defined as a combination of adaptive problem solving, stellar team efforts, and good leadership that leads to the company’s sustainable growth, improving its competitiveness in the market.
Waste Reduction (Muri, Mura, Muda)
Muda, Mura, and Muri are terms often used together in the Toyota Production System (and called the Three Ms) that collectively describe wasteful practices to be eliminated.
World Class Visual Workplace
Effective visual management will engage teams within the workforce. With teams fully engaged and armed with the key information and knowledge, the main aims for implementing a visual management strategy can be witnessed – to drive improvement, eliminate waste, improve safety and increase quality.
Implementation of DWM
DWM allows clear visibility of performances objectively and helps the cross-functional team focus on improvements. It helps to spot deviations from the target, get the relevant stakeholders involved in the improvement actions, and fix the problem rapidly.
Increasing Asset Efficiency
The most important benefit of asset management is that it provides a structured framework for investment planning that delivers the most cost-effective solutions for delivering acceptable levels of service over the entire asset life-cycle at minimal risk.
Lubrication Excellence
The benefits of a well-executed lubrication management system are numerous and real : decrease in maintenance costs, increase in the lifespan of equipment, reduced energy consumption, improvement in equipment availability, enhanced maintenance team productivity etc.
KAIZEN Implementation
Kaizen is about decreasing waste by eliminating overproduction, improving quality, being more efficient, having less idle time, and reducing unnecessary activities. All these translate to cost savings, and can turn potential losses into profits.
Operation & Maintenance Contracts
Plant Operation & Maintenance contracts manufacturing industries, especially aerospace, automotive, building products, heavy equipment, consumer packaged goods, paper/pulp and tire/rubber fields.